SMT menggunakan analisis dan solusi rongga pengelasan reflow udara pasta solder konvensional (Edisi Esensi 2023), Anda layak mendapatkannya!
1. Perkenalan

Pada rakitan papan sirkuit, pasta solder dicetak pada bantalan solder papan sirkuit terlebih dahulu, kemudian berbagai komponen elektronik ditempelkan.Akhirnya, setelah tungku reflow, butiran timah dalam pasta solder dilebur dan semua jenis komponen elektronik serta bantalan solder pada papan sirkuit dilas bersama untuk mewujudkan perakitan submodul listrik.Surfacemounttechnology (sMT) semakin banyak digunakan dalam produk pengemasan dengan kepadatan tinggi, seperti paket tingkat sistem (siP), perangkat ballgridarray (BGA), dan power bare Chip, paket tanpa pin datar persegi (quad aatNo-lead, disebut sebagai QFN ) perangkat.
Karena karakteristik proses dan bahan pengelasan pasta solder, setelah pengelasan reflow pada perangkat permukaan solder yang besar ini, akan terdapat lubang pada area pengelasan solder, yang akan mempengaruhi sifat listrik, sifat termal dan sifat mekanik kinerja produk, dan bahkan menyebabkan kegagalan produk, oleh karena itu, untuk memperbaiki rongga las reflow pasta solder telah menjadi proses dan masalah teknis yang harus dipecahkan, beberapa peneliti telah menganalisis dan mempelajari penyebab rongga las bola solder BGA, dan memberikan solusi perbaikan, solder konvensional proses pengelasan paste reflow area pengelasan QFN lebih besar dari 10mm2 atau area pengelasan lebih besar dari 6 mm2 solusi bare chip kurang.
Gunakan pengelasan Preformsolder dan pengelasan tungku refluks vakum untuk memperbaiki lubang las.Solder prefabrikasi memerlukan peralatan khusus untuk mengarahkan fluks.Misalnya, chip diimbangi dan dimiringkan secara serius setelah chip ditempatkan langsung pada solder prefabrikasi.Jika chip pemasangan fluks adalah reflow dan titik, prosesnya meningkat dua kali reflow, dan biaya solder prefabrikasi dan bahan fluks jauh lebih tinggi daripada pasta solder.
Peralatan refluks vakum lebih mahal, kapasitas vakum ruang vakum independen sangat rendah, kinerja biaya tidak tinggi, dan masalah percikan timah serius, yang merupakan faktor penting dalam penerapan kepadatan tinggi dan nada kecil. produk.Dalam makalah ini, berdasarkan proses pengelasan reflow pasta solder konvensional, proses pengelasan reflow sekunder baru dikembangkan dan diperkenalkan untuk memperbaiki rongga pengelasan dan memecahkan masalah ikatan dan retak segel plastik yang disebabkan oleh rongga pengelasan.
2 Pasta solder mencetak rongga pengelasan reflow dan mekanisme produksi
2.1 Rongga pengelasan
Setelah pengelasan reflow, produk diuji di bawah sinar-X.Lubang-lubang di zona pengelasan dengan warna lebih terang ditemukan karena kurangnya solder pada lapisan pengelasan, seperti yang ditunjukkan pada Gambar 1
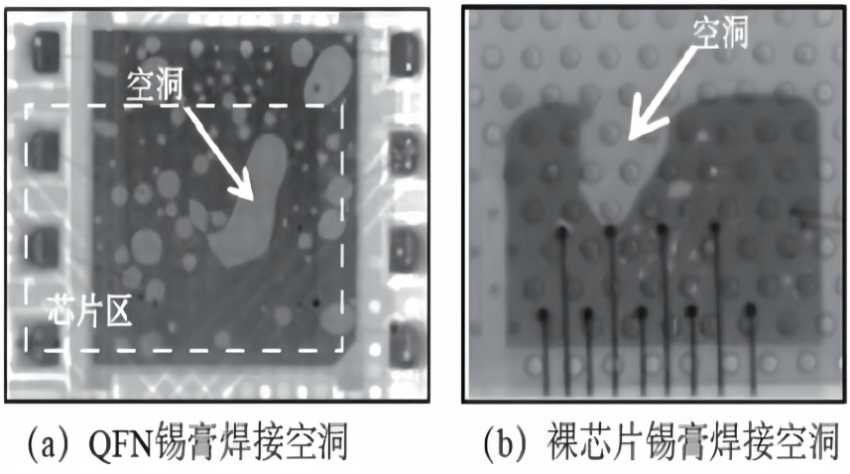
Deteksi sinar-X pada lubang gelembung
2.2 Mekanisme pembentukan rongga las
Mengambil contoh pasta solder sAC305, komposisi dan fungsi utama ditunjukkan pada Tabel 1. Fluks dan manik-manik timah diikat menjadi satu dalam bentuk pasta.Rasio berat solder timah terhadap fluks adalah sekitar 9:1, dan rasio volume sekitar 1:1.
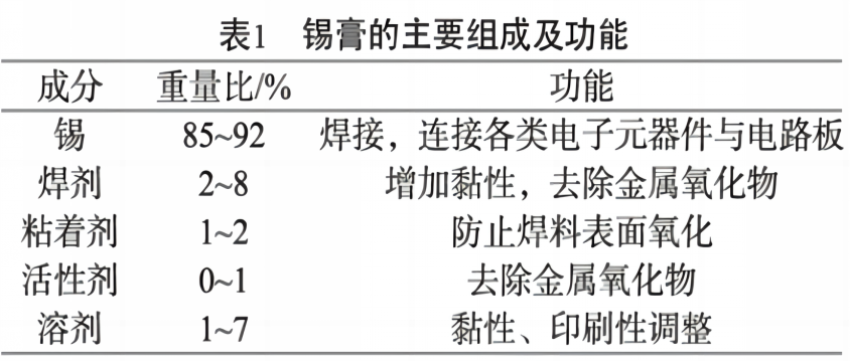
Setelah pasta solder dicetak dan dipasang dengan berbagai komponen elektronik, pasta solder akan mengalami empat tahap yaitu pemanasan awal, aktivasi, refluks dan pendinginan saat melewati tungku refluks.Keadaan pasta solder juga berbeda dengan suhu yang berbeda dalam tahapan yang berbeda, seperti yang ditunjukkan pada Gambar 2.
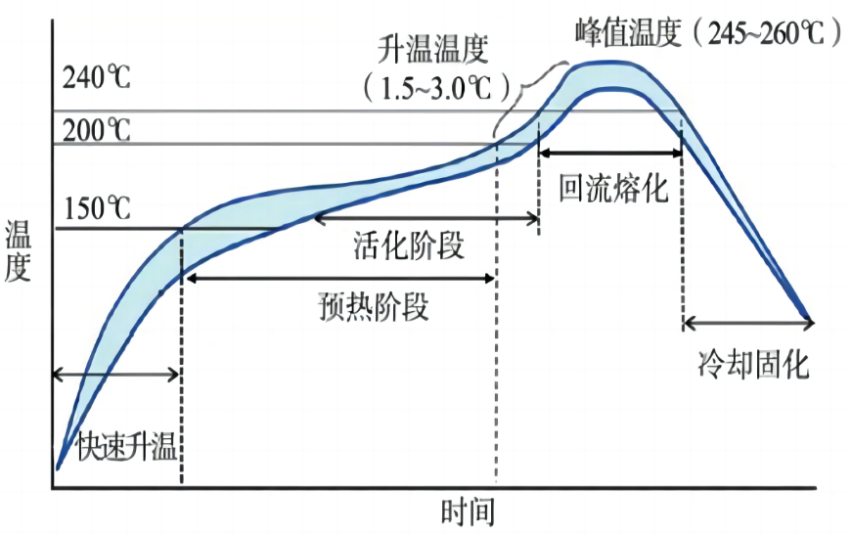
Referensi profil untuk setiap area penyolderan reflow
Pada tahap pemanasan awal dan aktivasi, komponen volatil pada fluks pasta solder akan menguap menjadi gas saat dipanaskan.Pada saat yang sama, gas akan dihasilkan ketika oksida pada permukaan lapisan pengelasan dihilangkan.Beberapa dari gas ini akan menguap dan meninggalkan pasta solder, dan manik-manik solder akan mengembun karena penguapan fluks.Pada tahap refluks, sisa fluks dalam pasta solder akan menguap dengan cepat, manik-manik timah akan meleleh, sejumlah kecil gas fluks yang mudah menguap dan sebagian besar udara di antara manik-manik timah tidak akan tersebar pada waktunya, dan sisa di dalam timah cair dan di bawah tekanan timah cair adalah struktur sandwich hamburger dan ditangkap oleh bantalan solder papan sirkuit dan komponen elektronik, dan gas yang dibungkus dalam timah cair sulit untuk dilepaskan hanya dengan daya apung ke atas. Waktu leleh atas sangat pendek.Ketika timah cair mendingin dan menjadi timah padat, pori-pori muncul pada lapisan pengelasan dan terbentuk lubang solder, seperti terlihat pada Gambar 3.
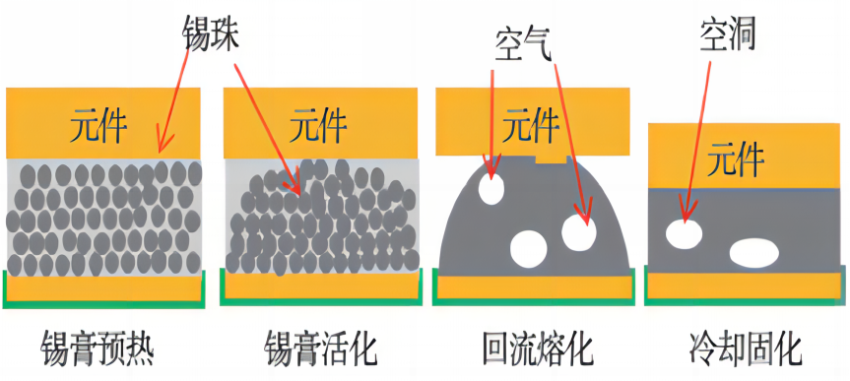
Diagram skema kekosongan yang dihasilkan oleh pengelasan reflow pasta solder
Akar penyebab rongga pengelasan adalah udara atau gas mudah menguap yang dibungkus pasta solder setelah peleburan tidak sepenuhnya habis.Faktor-faktor yang mempengaruhinya antara lain bahan pasta solder, bentuk cetakan pasta solder, jumlah cetakan pasta solder, suhu refluks, waktu refluks, ukuran pengelasan, struktur dan lain sebagainya.
3. Verifikasi faktor-faktor yang mempengaruhi lubang pengelasan reflow pencetakan pasta solder
Uji QFN dan bare chip digunakan untuk memastikan penyebab utama rongga pengelasan reflow, dan untuk menemukan cara memperbaiki rongga pengelasan reflow yang dicetak dengan pasta solder.Profil produk pengelasan reflow pasta solder QFN dan bare chip ditunjukkan pada Gambar 4, ukuran permukaan pengelasan QFN adalah 4.4mmx4.1mm, permukaan pengelasan adalah lapisan kaleng (100% timah murni);Ukuran pengelasan chip telanjang adalah 3.0mmx2.3mm, lapisan pengelasannya adalah lapisan bimetalik nikel-vanadium tergagap, dan lapisan permukaannya adalah vanadium.Bantalan las substratnya adalah pencelupan emas nikel-paladium tanpa listrik, dan ketebalannya 0,4μm/0,06μm/0,04μm.Pasta solder yang digunakan SAC305, peralatan pencetakan pasta solder adalah DEK Horizon APIx, peralatan tungku refluks adalah BTUPyramax150N, dan peralatan x-ray adalah DAGExD7500VR.
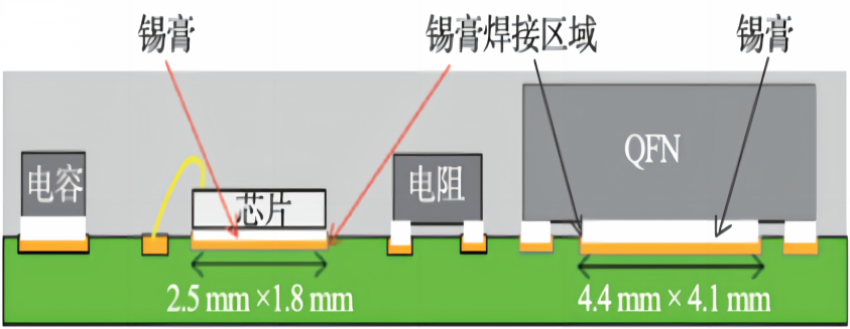
Gambar pengelasan QFN dan bare chip
Untuk memudahkan perbandingan hasil pengujian, pengelasan reflow dilakukan pada kondisi pada Tabel 2.
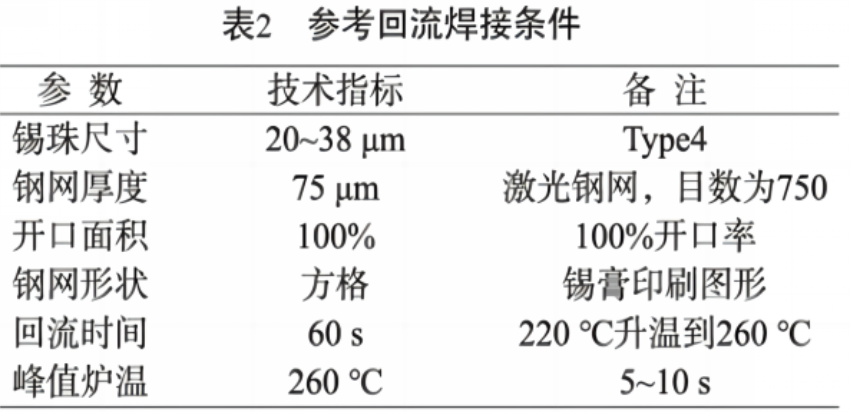
Tabel kondisi pengelasan reflow
Setelah pemasangan permukaan dan pengelasan reflow selesai, lapisan pengelasan terdeteksi dengan sinar-X, dan ditemukan adanya lubang besar pada lapisan pengelasan di bagian bawah QFN dan bare chip, seperti yang ditunjukkan pada Gambar 5.
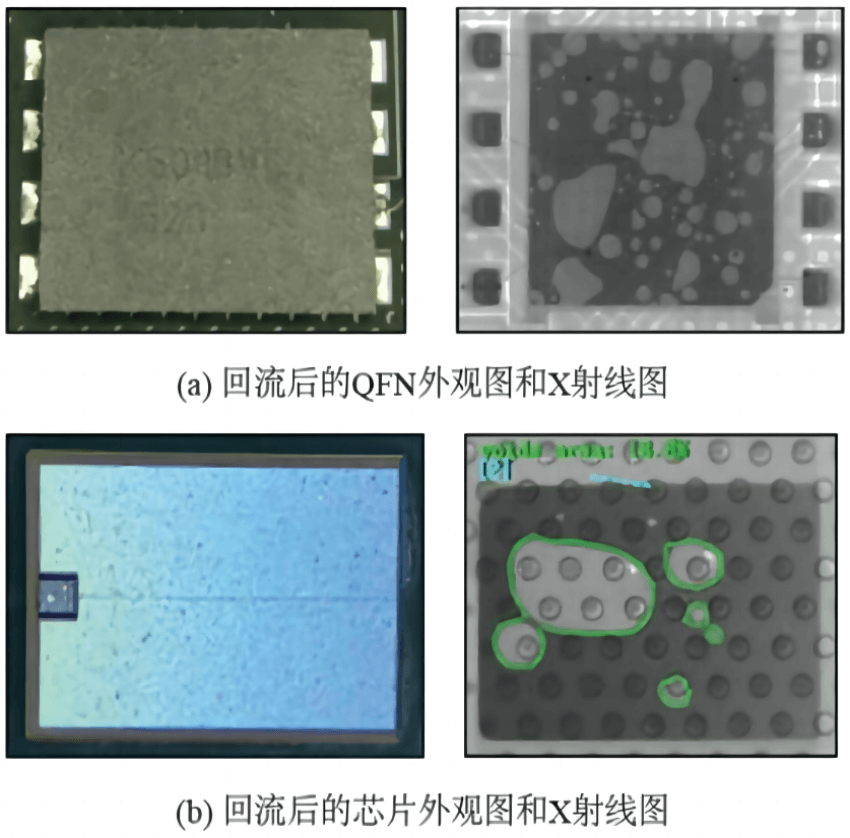
QFN dan Chip Hologram (sinar-X)
Karena ukuran manik timah, ketebalan jaring baja, laju luas bukaan, bentuk jaring baja, waktu refluks, dan suhu puncak tungku semuanya akan mempengaruhi rongga pengelasan reflow, ada banyak faktor yang mempengaruhi, yang akan diverifikasi langsung dengan uji DOE, dan jumlah percobaan. kelompok akan menjadi terlalu besar.Penting untuk menyaring dan menentukan faktor-faktor utama yang mempengaruhi secara cepat melalui uji perbandingan korelasi, dan kemudian mengoptimalkan lebih lanjut faktor-faktor yang mempengaruhi utama melalui DOE.
3.1 Dimensi lubang solder dan manik-manik timah pasta solder
Dengan uji pasta solder SAC305 tipe 3 (ukuran manik 25-45 μm), kondisi lainnya tetap tidak berubah.Setelah reflow, lubang pada lapisan solder diukur dan dibandingkan dengan pasta solder tipe 4.Ditemukan bahwa lubang-lubang pada lapisan solder tidak berbeda secara signifikan antara kedua jenis pasta solder, yang menunjukkan bahwa pasta solder dengan ukuran manik yang berbeda tidak memiliki pengaruh yang jelas terhadap lubang-lubang pada lapisan solder, yang bukan merupakan faktor yang mempengaruhi. seperti yang ditunjukkan pada Gambar.6 Seperti yang ditunjukkan.
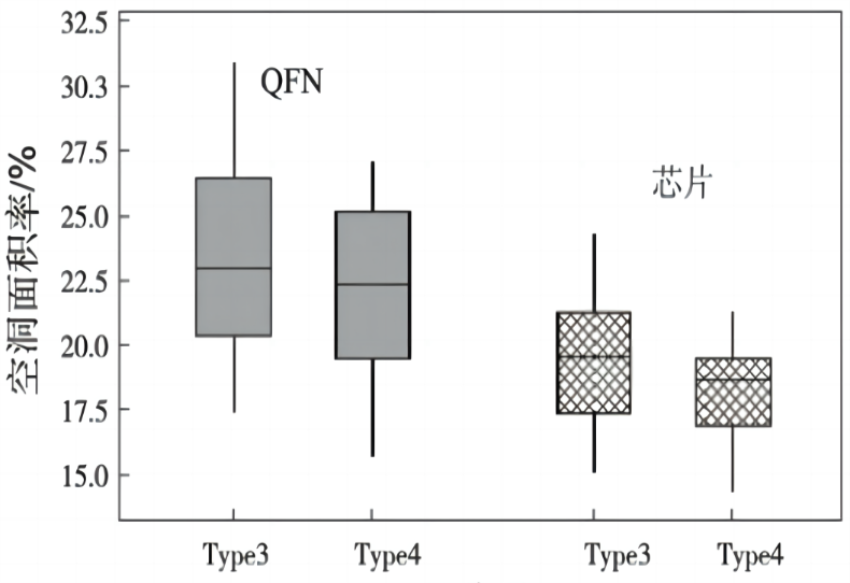
Perbandingan lubang serbuk timah metalik dengan ukuran partikel yang berbeda
3.2 Ketebalan rongga pengelasan dan jaring baja cetak
Setelah reflow, luas rongga lapisan yang dilas diukur dengan jaring baja cetak dengan ketebalan 50 μm, 100 μm dan 125 μm, dan kondisi lainnya tetap tidak berubah.Ditemukan bahwa pengaruh perbedaan ketebalan jaring baja (pasta solder) pada QFN dibandingkan dengan jaring baja cetak dengan ketebalan 75 μm. Seiring dengan bertambahnya ketebalan jaring baja, luas rongga secara bertahap berkurang secara perlahan.Setelah mencapai ketebalan tertentu (100μm), luas rongga akan berbalik dan mulai bertambah seiring bertambahnya ketebalan jaring baja, seperti terlihat pada Gambar 7.
Hal ini menunjukkan bahwa ketika jumlah pasta solder ditingkatkan, timah cair dengan refluks ditutupi oleh chip, dan saluran keluar sisa udara hanya sempit di empat sisi.Ketika jumlah pasta solder diubah, saluran keluar sisa udara juga meningkat, dan ledakan instan udara yang terbungkus dalam timah cair atau gas mudah menguap yang keluar dari timah cair akan menyebabkan timah cair terciprat di sekitar QFN dan chip.
Pengujian menemukan bahwa dengan bertambahnya ketebalan jaring baja, pecahnya gelembung yang disebabkan oleh keluarnya udara atau gas yang mudah menguap juga akan meningkat, dan kemungkinan percikan timah di sekitar QFN dan serpihan juga akan meningkat.
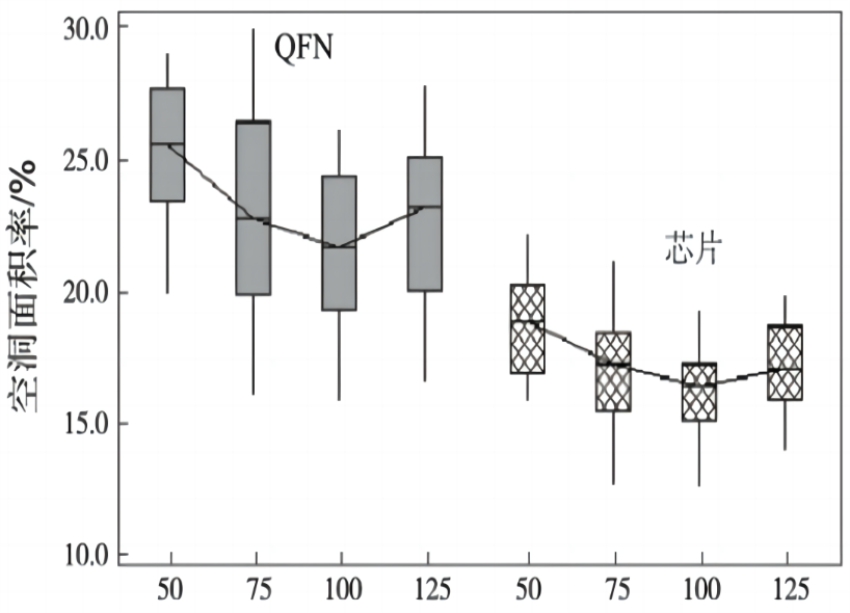
Perbandingan lubang pada jaring baja dengan ketebalan berbeda
3.3 Rasio luas rongga pengelasan dan bukaan jaring baja
Jaring baja cetak dengan tingkat pembukaan 100%, 90% dan 80% telah diuji, dan kondisi lainnya tetap tidak berubah.Setelah reflow, luas rongga lapisan yang dilas diukur dan dibandingkan dengan jaring baja cetak dengan tingkat pembukaan 100%.Ditemukan bahwa tidak ada perbedaan yang signifikan pada rongga lapisan yang dilas pada kondisi kecepatan pembukaan 100% dan 90% 80%, seperti terlihat pada Gambar 8.
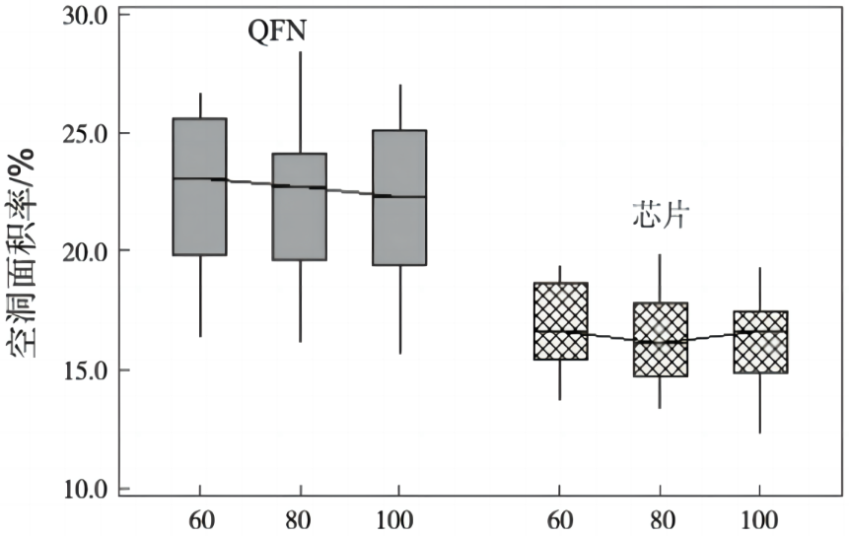
Perbandingan rongga pada area bukaan berbeda dari jaring baja yang berbeda
3.4 Rongga yang dilas dan bentuk jaring baja yang dicetak
Dengan uji bentuk pencetakan pasta solder strip b dan kisi miring c, kondisi lainnya tetap tidak berubah.Setelah reflow, luas rongga lapisan las diukur dan dibandingkan dengan bentuk pencetakan grid a.Terlihat bahwa tidak terdapat perbedaan yang signifikan pada rongga lapisan pengelasan pada kondisi grid, strip dan grid miring, seperti terlihat pada Gambar 9.
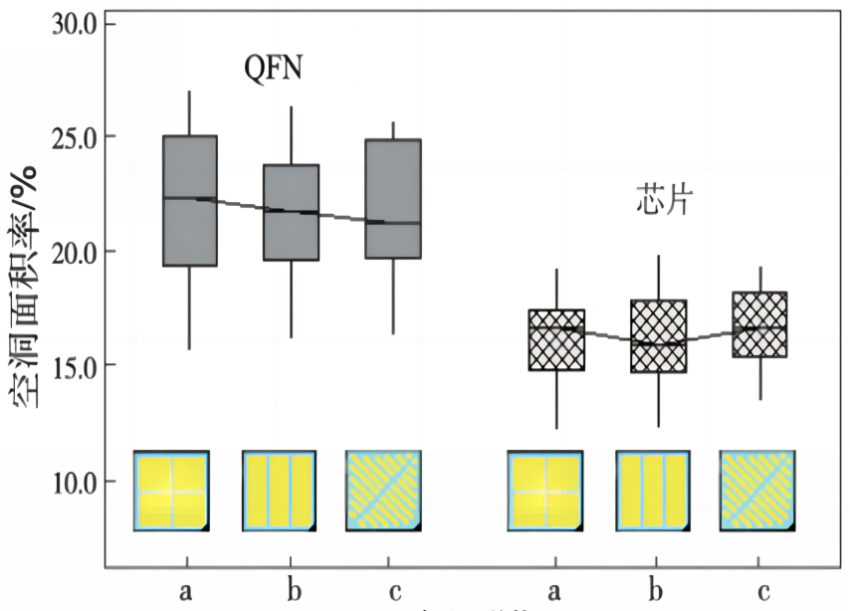
Perbandingan lubang dalam mode pembukaan jaring baja yang berbeda
3.5 Rongga pengelasan dan waktu refluks
Setelah pengujian waktu refluks yang berkepanjangan (70 detik, 80 detik, 90 detik), kondisi lain tetap tidak berubah, lubang pada lapisan pengelasan diukur setelah refluks, dan dibandingkan dengan waktu refluks 60 detik, ditemukan bahwa dengan peningkatan waktu refluks, luas lubang pengelasan berkurang, tetapi amplitudo reduksi secara bertahap menurun seiring bertambahnya waktu, seperti yang ditunjukkan pada Gambar 10. Hal ini menunjukkan bahwa dalam kasus waktu refluks yang tidak mencukupi, peningkatan waktu refluks kondusif untuk meluapnya udara secara penuh. dibungkus dengan timah cair cair, namun setelah waktu refluks bertambah hingga waktu tertentu, udara yang dibungkus dalam timah cair sulit untuk meluap kembali.Waktu refluks merupakan salah satu faktor yang mempengaruhi rongga pengelasan.
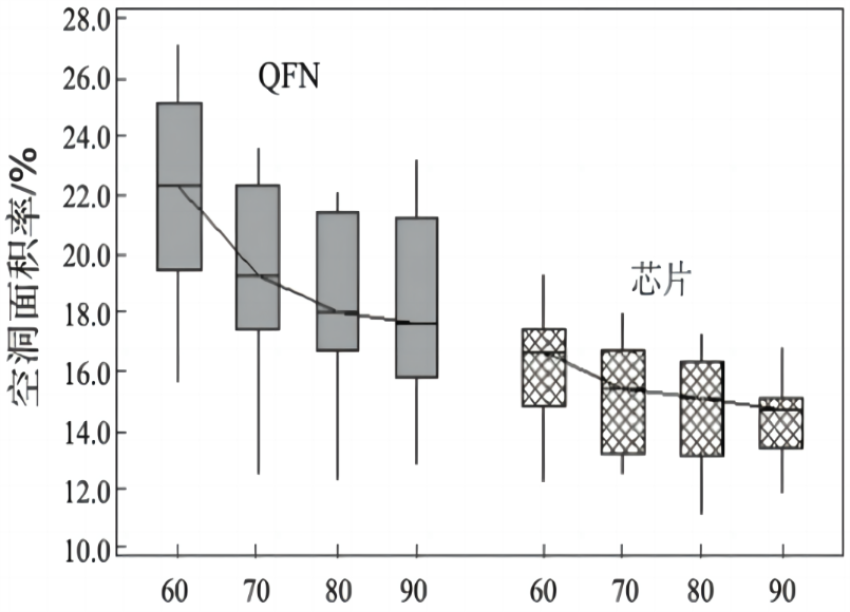
Batalkan perbandingan jangka waktu refluks yang berbeda
3.6 Rongga pengelasan dan suhu puncak tungku
Dengan uji suhu tungku puncak 240 ℃ dan 250 ℃ dan kondisi lainnya tidak berubah, luas rongga lapisan yang dilas diukur setelah reflow, dan dibandingkan dengan suhu tungku puncak 260 ℃, ditemukan bahwa dalam kondisi suhu tungku puncak yang berbeda, rongga lapisan QFN dan chip yang dilas tidak mengalami perubahan yang signifikan, seperti yang ditunjukkan pada Gambar 11. Hal ini menunjukkan bahwa suhu puncak tungku yang berbeda tidak memiliki pengaruh yang jelas terhadap QFN dan lubang pada lapisan pengelasan chip, yang bukan merupakan faktor yang mempengaruhi.
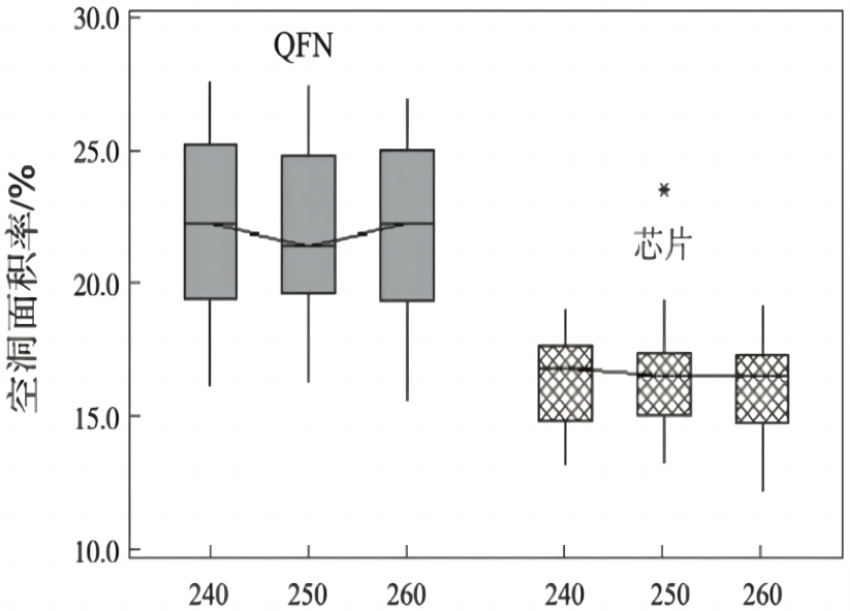
Batalkan perbandingan suhu puncak yang berbeda
Pengujian di atas menunjukkan bahwa faktor signifikan yang mempengaruhi rongga lapisan las QFN dan chip adalah waktu refluks dan ketebalan jaring baja.
4 perbaikan rongga pengelasan reflow pencetakan pasta solder
Tes 4.1DOE untuk meningkatkan rongga pengelasan
Lubang pada lapisan pengelasan QFN dan chip diperbaiki dengan mencari nilai optimal dari faktor pengaruh utama (waktu refluks dan ketebalan jaring baja).Pasta solder adalah SAC305 tipe 4, bentuk jaring baja adalah tipe kisi (derajat pembukaan 100%), suhu tungku puncak adalah 260 ℃, dan kondisi pengujian lainnya sama dengan peralatan uji.Uji DOE dan hasilnya ditunjukkan pada Tabel 3. Pengaruh ketebalan jaring baja dan waktu refluks pada lubang las QFN dan chip ditunjukkan pada Gambar 12. Melalui analisis interaksi faktor-faktor yang mempengaruhi utama, diketahui bahwa menggunakan ketebalan jaring baja 100 μm dan waktu refluks 80 detik dapat secara signifikan mengurangi rongga pengelasan QFN dan chip.Tingkat rongga pengelasan QFN berkurang dari maksimum 27,8% menjadi 16,1%, dan tingkat rongga pengelasan chip berkurang dari maksimum 20,5% menjadi 14,5%.
Dalam pengujian tersebut, 1000 produk diproduksi dalam kondisi optimal (ketebalan jaring baja 100 μm, waktu refluks 80 detik), dan laju rongga pengelasan 100 QFN dan chip diukur secara acak.Rata-rata tingkat rongga pengelasan QFN adalah 16,4%, dan rata-rata tingkat rongga pengelasan chip adalah 14,7%. Tingkat rongga las chip dan chip jelas berkurang.
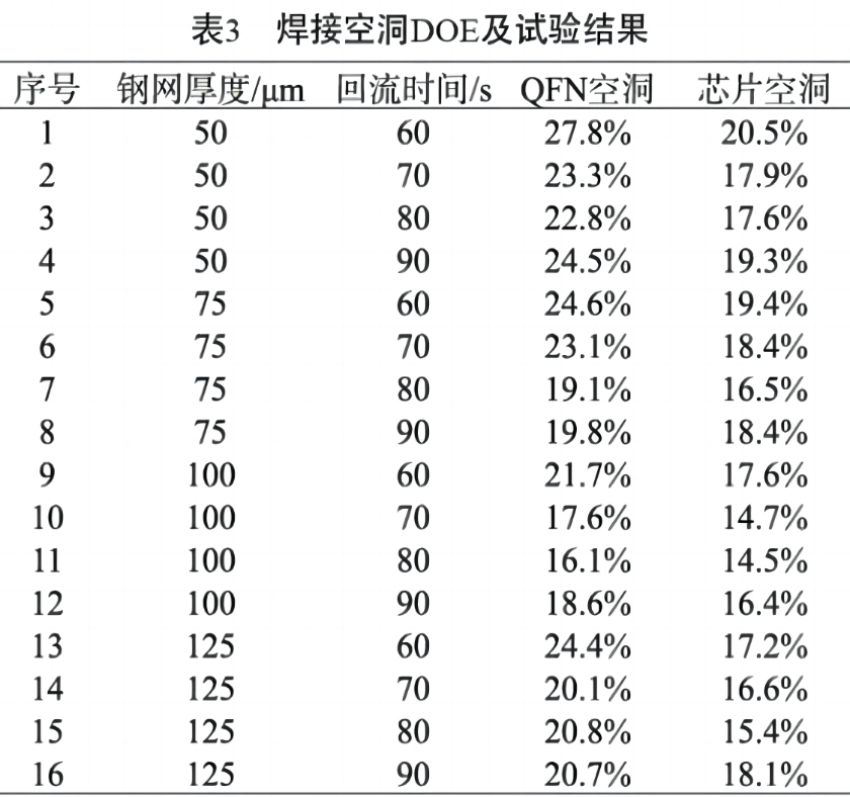
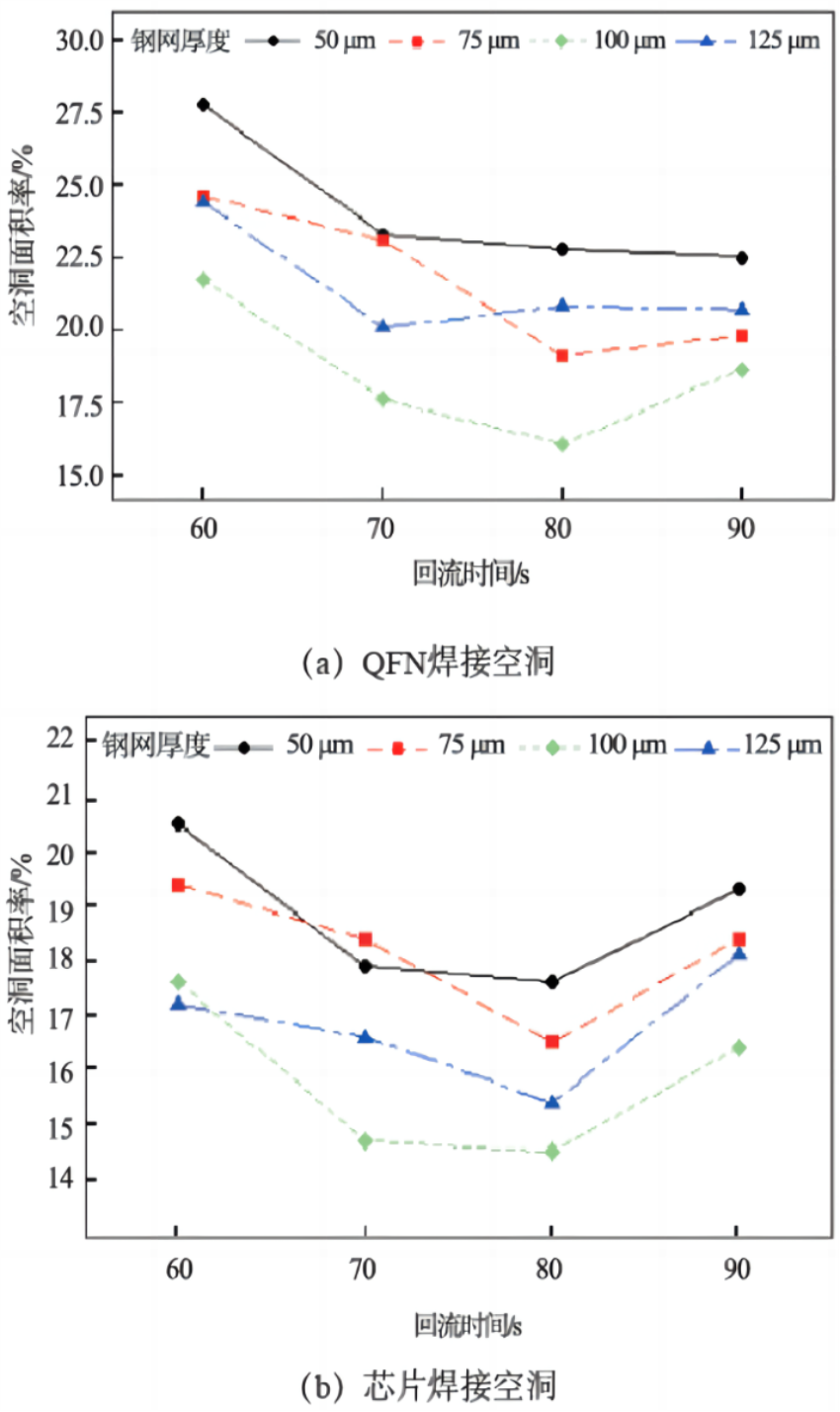
4.2 Proses baru memperbaiki rongga pengelasan
Situasi produksi aktual dan pengujian menunjukkan bahwa ketika area rongga pengelasan di bagian bawah chip kurang dari 10%, masalah retak posisi rongga chip tidak akan terjadi selama pengikatan dan pencetakan timbal.Parameter proses yang dioptimalkan oleh DOE tidak dapat memenuhi persyaratan analisis dan penyelesaian lubang pada pengelasan reflow pasta solder konvensional, dan laju area rongga pengelasan pada chip perlu dikurangi lebih lanjut.
Karena chip yang dilapisi solder mencegah gas dalam solder keluar, laju lubang di bagian bawah chip semakin berkurang dengan menghilangkan atau mengurangi gas yang dilapisi solder.Proses baru pengelasan reflow dengan dua pencetakan pasta solder diadopsi: satu pencetakan pasta solder, satu reflow tidak mencakup QFN dan chip kosong yang mengeluarkan gas dalam solder;Proses spesifik pencetakan pasta solder sekunder, patch dan refluks sekunder ditunjukkan pada Gambar 13.
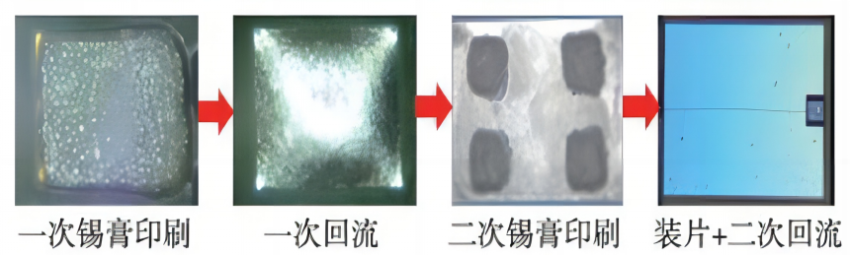
Ketika pasta solder setebal 75μm dicetak untuk pertama kalinya, sebagian besar gas dalam solder tanpa penutup chip keluar dari permukaan, dan ketebalan setelah refluks sekitar 50μm.Setelah refluks primer selesai, kotak-kotak kecil dicetak pada permukaan solder padat yang didinginkan (untuk mengurangi jumlah pasta solder, mengurangi jumlah tumpahan gas, mengurangi atau menghilangkan percikan solder), dan pasta solder dengan ketebalan 50 μm (hasil pengujian di atas menunjukkan bahwa 100 μm adalah yang terbaik, jadi ketebalan pencetakan sekunder adalah 100 μm.50 μm=50 μm), lalu pasang chip, lalu kembalikan setelah 80 detik.Hampir tidak ada lubang pada solder setelah pencetakan pertama dan reflow, dan pasta solder pada pencetakan kedua kecil, dan lubang pengelasannya kecil, seperti yang ditunjukkan pada Gambar 14.
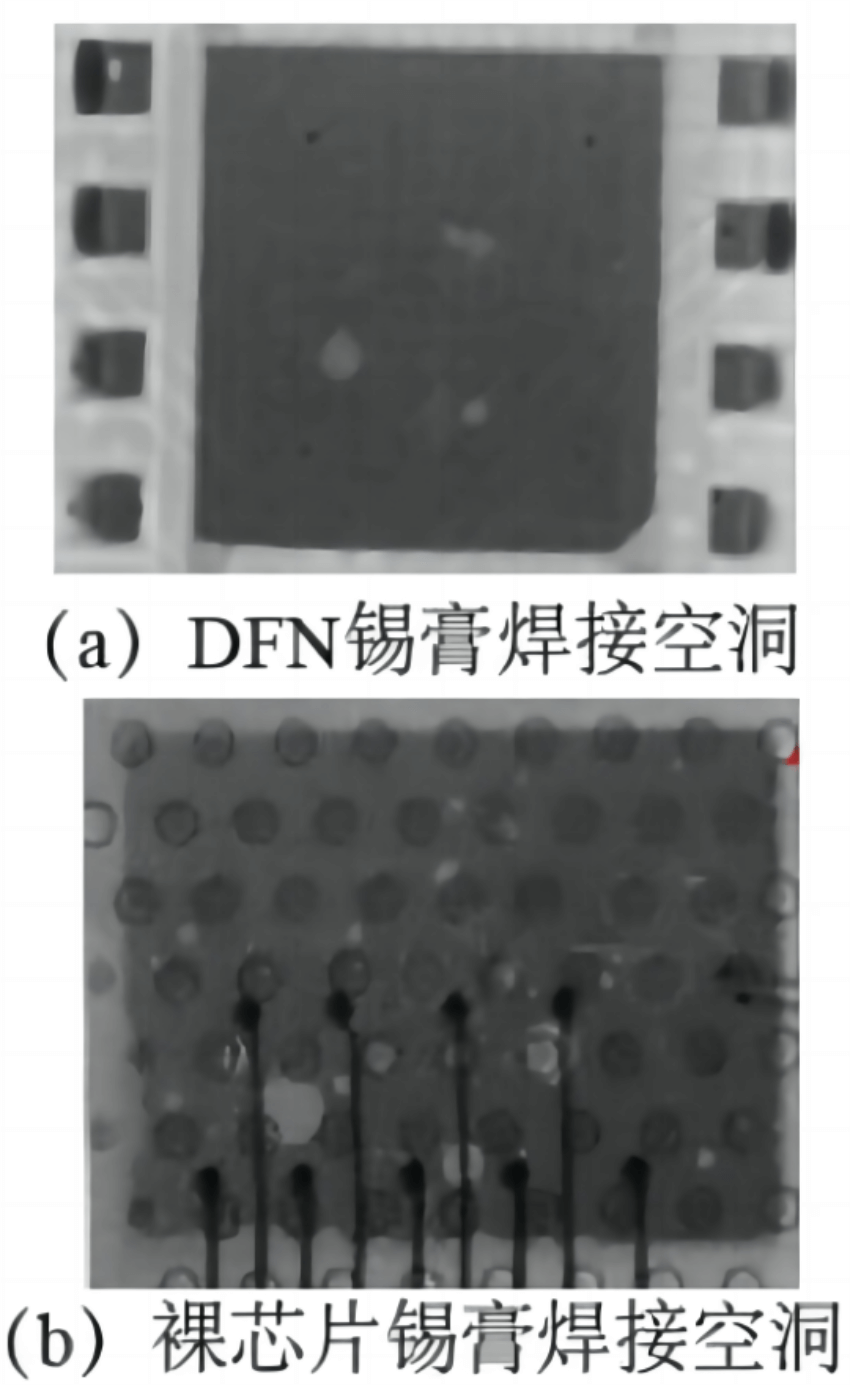
Setelah dua cetakan pasta solder, gambar berongga
4.3 Verifikasi efek rongga pengelasan
Produksi 2000 produk (ketebalan jaring baja pencetakan pertama adalah 75 μm, ketebalan jaring baja pencetakan kedua adalah 50 μm), kondisi lain tidak berubah, pengukuran acak 500 QFN dan laju rongga pengelasan chip, menemukan bahwa proses baru setelah refluks pertama tidak ada rongga, setelah refluks kedua QFN Tingkat rongga pengelasan maksimum adalah 4,8%, dan tingkat rongga pengelasan maksimum chip adalah 4,1%.Dibandingkan dengan proses pengelasan pencetakan pasta tunggal asli dan proses yang dioptimalkan DOE, rongga pengelasan berkurang secara signifikan, seperti yang ditunjukkan pada Gambar 15. Tidak ada retakan chip yang ditemukan setelah uji fungsional semua produk.
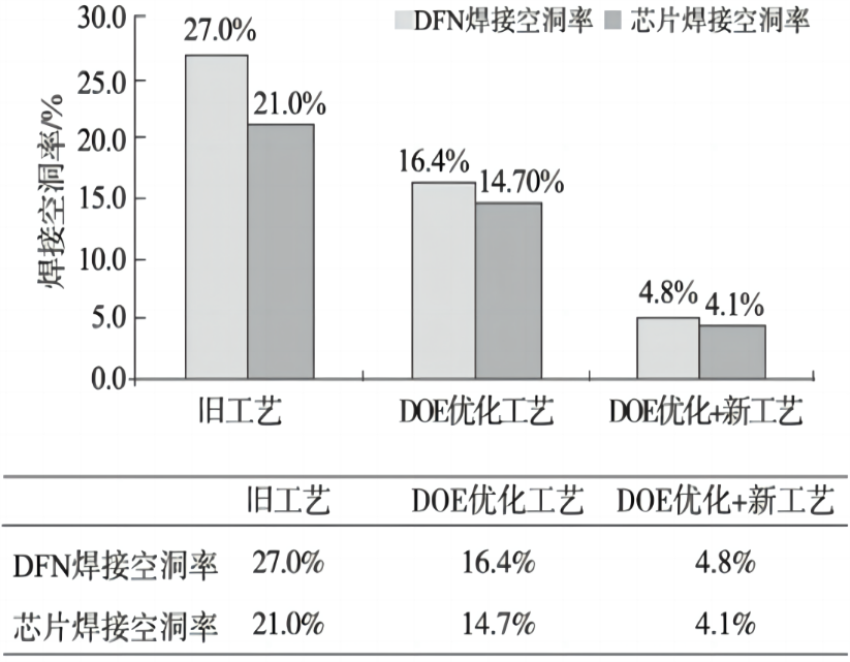
5 Ringkasan
Optimalisasi jumlah pencetakan pasta solder dan waktu refluks dapat mengurangi luas rongga pengelasan, namun laju rongga pengelasan masih besar.Menggunakan dua teknik pengelasan reflow pencetakan pasta solder dapat secara efektif dan memaksimalkan tingkat rongga pengelasan.Area pengelasan chip telanjang sirkuit QFN masing-masing dapat berukuran 4,4mm x4.1mm dan 3.0mm x2.3mm dalam produksi massal. Tingkat rongga pengelasan reflow dikontrol di bawah 5%, yang meningkatkan kualitas dan keandalan pengelasan reflow.Penelitian dalam makalah ini memberikan referensi penting untuk memperbaiki masalah rongga pengelasan pada permukaan pengelasan yang luas.